As a bearing application engineer with years of experience serving equipment manufacturers and industrial distributors, I often get asked: “Which type of bearing should I use for high-precision transmission applications?” It’s a simple question with a complex answer. Choosing the right precision transmission bearing depends on technical factors such as load direction, speed, rigidity, heat generation, installation constraints—and most importantly—the industry-specific performance demands.
In this article, I’ll explain the main types of precision transmission bearings, their internal structure and functional characteristics, and the industries and machines where each type is most commonly applied. This is a professional-level reference designed for bearing wholesalers, OEM buyers, distributors, and end users.
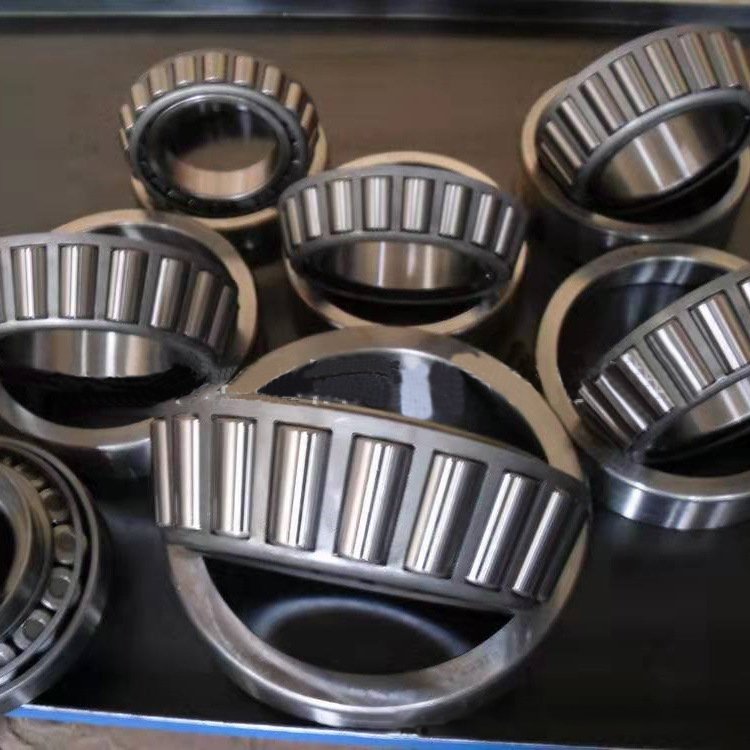
What Are Precision Transmission Bearings?
Precision transmission bearings are used in applications where rotational accuracy, low vibration, high rigidity, and tight axial and radial tolerances are non-negotiable. These are not general-purpose bearings. They are manufactured under strict ISO/ABEC precision grades (typically P5, P4, P2 / ABEC 5, 7, 9) and are used in systems where mechanical transmission accuracy directly affects system quality—like CNC machining, robotics, and aerospace.
Common Types of Precision Transmission Bearings
1. Angular Contact Ball Bearings
Structure & Function:
These bearings have raceways in the inner and outer rings that are displaced relative to each other in the direction of the bearing axis. This allows them to support both radial and unidirectional axial loads. When used in matched pairs or sets, they can handle axial loads in both directions and improve system rigidity.
Key Variants:
- Single-row for high-speed spindles
- Duplex pairs (DB, DF, DT) for combined loads
- Hybrid ceramic types for ultra-high-speed and reduced heat
Typical Applications:
- CNC machine spindles (metal cutting)
- Grinding machines
- Servo motor supports in robotics
- Electric vehicle gearboxes
2. Cylindrical Roller Bearings (High-Precision Type)
Structure & Function:
They use cylindrical rollers guided between raceways. Their point contact becomes line contact, offering superior radial load capacity and very low friction. Most have separable designs for easier mounting.
Functional Advantages:
- Handles heavy radial loads at high speed
- Low heat generation due to minimal sliding
- Minimal axial load support unless modified
Typical Applications:
- Main shafts in machine tools
- Precision gearboxes
- Industrial reducers
- Servo motor rear-end support
3. Tapered Roller Bearings (Precision Class)
Structure & Function:
These bearings use conical rollers and raceways, allowing them to bear combined axial and radial loads with high rigidity. Precision grades (CL3, CL0, J series) are ground for minimal runout.
Advantages:
- Excellent for shock load resistance
- Adjustable preload capability
- High axial and radial stiffness
Typical Applications:
- Automotive transmissions (especially in differential and gearboxes)
- High-precision vertical milling heads
- Gear reducers in robotic arms
4. Crossed Roller Bearings
Structure & Function:
Rollers are alternately arranged at 90° angles, allowing the bearing to support radial, axial, and moment loads simultaneously. They’re compact, with high rigidity and rotational accuracy.
Advantages:
- Space-saving structure
- High positioning accuracy
- Excellent for limited-space, high-load environments
Typical Applications:
- Robot rotary joints
- Precision indexing tables
- Aerospace simulation systems
- Semiconductor processing
5. Thrust Ball and Thrust Roller Bearings (Precision Grade)
Structure & Function:
Designed for pure axial load handling, these bearings have raceways perpendicular to the shaft. Ball versions are suitable for lower loads and high speeds, while roller types support heavier loads at slower speeds.
Variants:
- Angular contact thrust ball (for high axial precision)
- Thrust cylindrical roller (for heavy axial loads)
Typical Applications:
- Vertical lathe spindles
- Indexing tables
- Optical alignment systems
- Screw drives in injection molding machines
6. Needle Roller Bearings (Precision Type)
Structure & Function:
These bearings use long, thin rollers, providing a very high load capacity in compact designs. High-precision types are ground to tight tolerances and are used where space is constrained.
Limitations:
- Low-speed and moderate friction
- Suitable only for radial loads
Typical Applications:
- Robotic linear actuators
- Compact gear trains
- Aircraft actuation systems
Key Industries and Their Bearing Requirements
The following outlines how various industries select and implement specific types of precision transmission bearings based on their unique performance, load, and structural requirements.
1. Machine Tool Industry
- Used Bearings: Angular contact ball, cylindrical roller, tapered roller
- Application Notes: Spindle performance requires high-speed angular contact ball bearings with preload; rear support often uses cylindrical rollers for rigidity.
2. Automotive Industry (EV and Traditional)
- Used Bearings: Tapered roller, needle roller, angular contact ball
- Application Notes: Precision tapered roller bearings are used in transmission and differential shafts. EV motors use ceramic hybrid angular contact bearings for high-speed torque transfer.
3. Robotics and Automation
- Used Bearings: Crossed roller, angular contact ball, needle roller
- Application Notes: Crossed rollers are standard in rotating joints; servo actuators use angular contact ball bearings for precision; compact gearboxes benefit from needle rollers.
4. Aerospace and Defense
- Used Bearings: Crossed roller, thrust roller, angular contact ball
- Application Notes: Navigation and positioning systems require zero-backlash crossed roller bearings; actuators use angular and thrust bearings for high load accuracy.
5. Medical Equipment
- Used Bearings: Angular contact ball, crossed roller, thrust ball
- Application Notes: Quiet and clean operation is critical; non-magnetic angular contact or crossed roller bearings are used in imaging and diagnostic machines.
6. Semiconductor and Photonics
- Used Bearings: Crossed roller, air bearings (non-contact), angular contact
- Application Notes: Requires ultra-high positioning accuracy and clean operation—crossed rollers are widely applied in wafer processing and photonics alignment systems.
Conclusion
Precision transmission bearings are mission-critical components in every advanced mechanical system. As a bearing engineer, I recommend:
- Assessing load direction, speed, and system dynamics
- Matching bearing type to industry-specific requirements
- Choosing precision grades P4 or P2 for maximum performance
- Sourcing from technically certified manufacturers only
If you’re a wholesaler, system integrator, or OEM, understanding the differences between these bearings is key to enhancing machine performance and securing long-term reliability for your customers.