As a bearing application engineer, I’m often asked by OEMs, end users, and distributors the same fundamental question:
“Should I choose ceramic ball bearings or steel ball bearings—and what’s the real difference between them?”
The choice between these two types of bearings can directly affect machine speed, load capacity, thermal stability, and service life. So let’s dive into the technical and functional differences—beyond just the material composition—so you can make the right decision for your specific application.
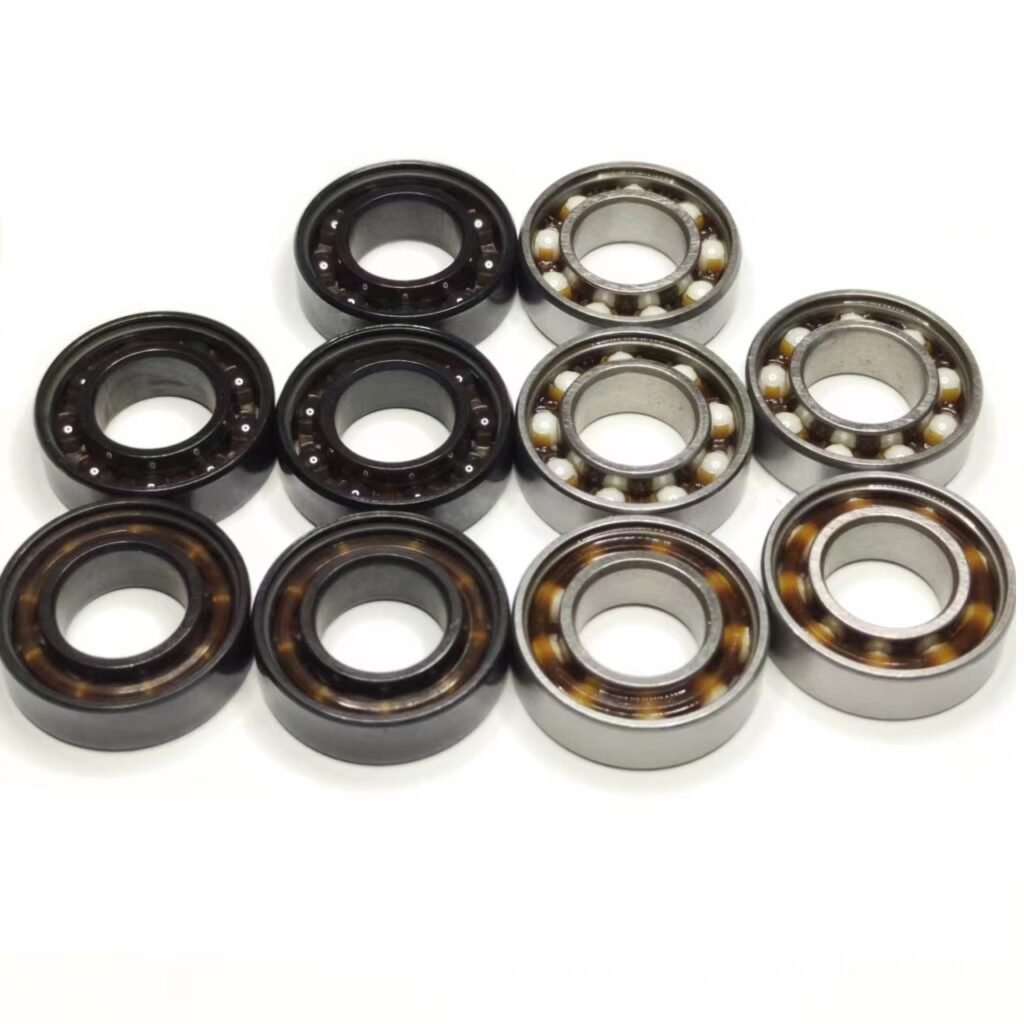
1. Core Material Difference
The most obvious distinction is in the material used for the rolling elements—the balls.
- Steel Ball Bearings use precision balls made from high carbon chromium steel (typically AISI 52100).
- Ceramic Ball Bearings use balls made from silicon nitride (Si₃N₄) or zirconia (ZrO₂), with silicon nitride being more common in high-speed applications.
While both types often use steel races (in hybrid bearings), the balls themselves make all the difference in performance.
2. Speed and Performance Characteristics
Ceramic balls are significantly lighter than steel balls—roughly 60% less dense. This lower mass reduces centrifugal force during rotation, which is critical for high-speed applications like high-frequency spindles or turbo machinery.
From my hands-on experience:
- Ceramic ball bearings can operate at 30–50% higher speeds than steel counterparts.
- Reduced friction and heat generation in ceramic bearings lead to better performance under extreme RPMs.
If you’re building or maintaining ultra-high-speed equipment, ceramic is often the only viable choice.
3. Wear Resistance and Service Life
Ceramic materials are extremely hard—much harder than steel. This makes ceramic balls far more resistant to wear and surface fatigue, especially in demanding or dirty environments.
In applications where contamination is a risk (e.g., dry running or poor lubrication), ceramic bearings consistently outlast their steel counterparts.
Case example: In one CNC spindle upgrade project, switching to ceramic hybrid bearings extended the bearing life by 3X due to better resistance to lubrication breakdown and thermal stress.
4. Thermal Stability and Insulation
Here’s where ceramic bearings provide a unique advantage: they are electrically insulating. Unlike steel, silicon nitride does not conduct electricity.
This makes ceramic hybrid bearings ideal for:
- Electric motors prone to current leakage
- High-frequency spindles with inverter drive systems
- Applications where electrical pitting of steel bearings is a risk
Steel ball bearings, in contrast, can suffer electrical erosion, resulting in pitting and premature failure.
Additionally, ceramic balls expand much less under heat, maintaining tighter clearances and reducing thermal runout—essential for high-precision applications.
5. Cost and Application Suitability
Of course, ceramic bearings are more expensive—sometimes significantly more. But in my experience, that higher upfront cost is justified in critical applications where:
- Downtime is costly
- High speeds or thermal loads are unavoidable
- Precision and durability are paramount
- On the other hand, steel ball bearings are ideal for:
- General industrial use
- Moderate-speed and heavy-load environments
- Applications where cost-effectiveness is the priority
My Practical Advice
When choosing between ceramic and steel ball bearings, I always guide clients to focus on application needs, not material hype.
- For high-speed, high-precision, or electrically sensitive applications, ceramic is the clear winner.
- For general-purpose industrial machinery, pumps, or conveyors, high-quality steel ball bearings are more than sufficient.
Comparison Table: Ceramic Ball Bearings vs Steel Ball Bearings
Below is a professional comparison table summarizing the essential differences between ceramic ball bearings and steel ball bearings.
Feature | Ceramic Ball Bearings (Hybrid) | Steel Ball Bearings |
Ball Material | Silicon Nitride (Si₃N₄) or Zirconia (ZrO₂) | High Carbon Chromium Steel (AISI 52100) |
Density | ~40% of steel (lighter) | Heavier |
Speed Capability | ★★★★☆ (30–50% higher speed limit) | ★★☆☆☆ (standard speed range) |
Wear Resistance | ★★★★☆ (excellent in harsh or dry environments) | ★★☆☆☆ (good with proper lubrication) |
Electrical Insulation | Yes (non-conductive, protects from electric pitting) | No (conductive; prone to electrical erosion) |
Thermal Expansion | Low (maintains precision under heat) | Higher (may cause thermal runout) |
Lubrication Sensitivity | Less sensitive; runs cooler | Sensitive; requires stable lubrication film |
Noise & Vibration | Low; stable rotation | Slightly higher under same conditions |
Load Capacity | Similar (depends on race design) | Similar (depends on race design) |
Typical Applications | High-speed spindles, electric motors, aerospace | General machinery, pumps, industrial equipment |
Cost | Higher (premium-grade) | Lower (cost-effective) |
Final Thoughts
The essential difference between ceramic and steel ball bearings lies in how they perform under real-world stress—speed, temperature, electrical insulation, and wear. As an engineer, I’ve seen firsthand how selecting the right bearing type can increase machine performance, reduce downtime, and save long-term costs.
If you’re unsure which type suits your application best, don’t hesitate to reach out. With the right bearing, your equipment doesn’t just run—it excels.