As a bearing application engineer with years of experience working alongside machine tool OEMs, maintenance teams, and industrial distributors, I often get asked one critical question:
“Why do our machine tool bearings develop raceway spalling, even when the bearing seems properly installed?”
Raceway spalling is one of the most common and serious failure modes in high-precision bearings, especially in the demanding environment of machine tools. If left unchecked, it leads to vibration, loss of accuracy, increased noise, and eventual equipment failure. In this article, I’ll break down the key causes of raceway spalling and provide practical insights based on real-world cases.
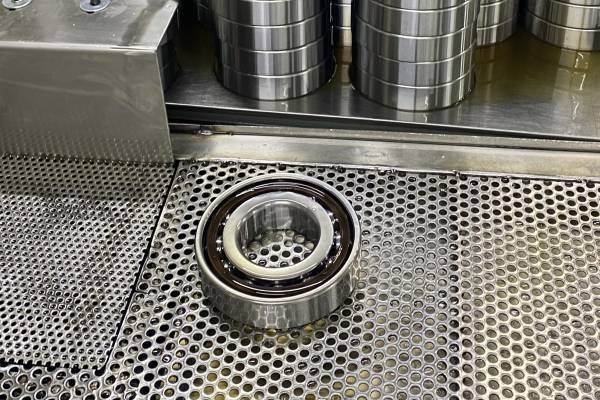
1. Fatigue from Overloading or Repeated Stress
The most fundamental cause of spalling is fatigue—caused by stresses exceeding the bearing’s dynamic load rating. In machine tools, especially in spindles or feed drives, moment loads and cutting forces often fluctuate. When a bearing is repeatedly stressed beyond its design threshold, small cracks form below the surface of the raceway. These cracks eventually propagate to the surface, causing material to break off—this is spalling.
Common causes:
- Oversized cutting tools or aggressive feed rates
- Improper preloading of angular contact bearings
- Unexpected impact loads (e.g., tool crashes)
My advice: Always verify the actual operating load conditions against bearing specifications. Don’t rely solely on catalog ratings—factor in preload effects and dynamic load variations.
2. Poor Lubrication or Contamination
In my experience, improper lubrication is one of the fastest ways to shorten bearing life. Inadequate lubrication leads to increased metal-to-metal contact, heat generation, and eventually micro-welding between rolling elements and raceways. This promotes micro-cracking and surface fatigue, leading to early spalling.
Contaminants—even microscopic ones like metal chips or abrasives—can embed into the raceway and act as stress concentrators, initiating spalling.
Typical signs:
- Darkened or discolored raceways
- Pitted or frosted appearance on the race surface
Best practices:
- Use the correct viscosity and lubrication type (grease or oil mist) as recommended by the bearing or machine manufacturer.
- Ensure seals and filters are intact and clean.
- Regularly monitor lubricant condition and replace when degraded.
3. Improper Mounting or Shaft/Housing Misalignment
Misalignment or incorrect mounting procedures often go unnoticed until failure occurs. When the inner and outer rings are not aligned properly with the shaft and housing, the rolling elements apply uneven stress to the raceways. This leads to localized overloading and stress concentration—again, a trigger for spalling.
Examples I’ve seen:
- Bearings mounted with excessive hammering or without proper heating
- Shaft shoulders that are not square to the axis
- Bearing seats with out-of-tolerance roundness or concentricity
Recommendation: Always use precision fitting tools and follow proper mounting techniques. For high-speed machine tools, even microns of misalignment can result in premature failure.
4. Corrosion and Moisture Ingress
Corrosion may not be the first suspect, but I’ve seen it contribute significantly to raceway degradation, especially in environments with high humidity, coolant leakage, or poor sealing. Rust particles act similarly to hard contaminants—damaging the raceway and accelerating fatigue spalling.
Prevention tips:
- Apply corrosion-resistant coatings when necessary
- Use sealed bearings in environments exposed to coolants
- Ensure proper drainage and ventilation in the housing design
5. Brinelling and False Brinelling
True brinelling occurs due to static overload or shock, leaving permanent indentations on the raceway. These indentations concentrate stress and act as initiation points for spalling.
False brinelling, on the other hand, happens during machine idle time when small vibrations cause micro-movement between the rolling elements and raceway, leading to wear marks that resemble brinelling.
Both conditions weaken the raceway and eventually cause material flaking.
Key tip: Use vibration dampers during transport or machine downtime. For machines that sit idle frequently, rotate the shaft periodically to distribute lubricant and reduce wear.
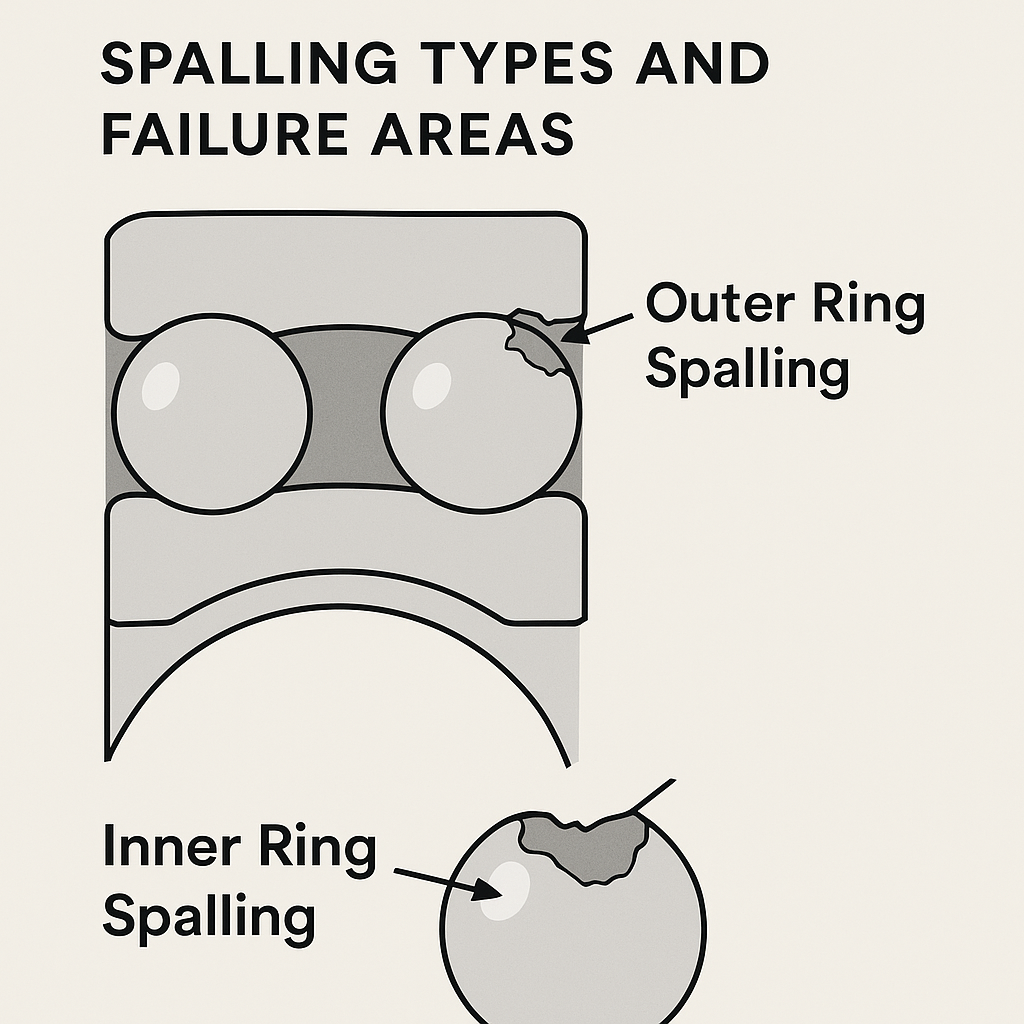
Final Thoughts
Raceway spalling is not just a material failure—it’s a signal that something is wrong in the system. As an engineer, I always emphasize root cause analysis before replacing a failed bearing. Swapping out the bearing without addressing the underlying issue is a short-term fix that invites long-term problems.
Whether you’re a machine tool user, a distributor advising clients, or a maintenance manager trying to reduce downtime, understanding these root causes empowers you to make smarter, more cost-effective decisions.
If you need technical support or help analyzing failed bearings, I’m always happy to offer insight. Preventing spalling starts with application-specific knowledge—and that’s where I can help.