Since 2016, due to the US government’s imposition of tariffs on some Chinese-made goods and the fourth migration of the global manufacturing industry, some manufacturing factories have moved from China to Vietnam or other Southeast Asian countries, but this is only the migration of some manufacturing industries. Some high-end manufacturing and high-tech manufacturing are still dominated by China. For example, there has been no major migration in the bearing manufacturing industry. But you who are in a foreign country may not know much about the current situation of Chinese manufacturing. When you are looking for a bearing supplier, you may be hesitating whether to purchase bearings in China or in Vietnam?
So as a member of the Chinese bearing manufacturing industry, I decided to write such an article today to let foreign buyers clearly understand the current situation of the Chinese bearing manufacturing industry.
This article makes a comprehensive, data-driven comparison of the bearing manufacturing industries in China and Vietnam to help international buyers make wise decisions.
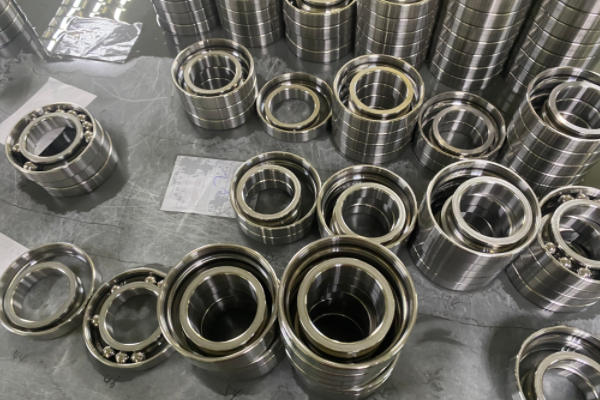
1. The Scale of Bearing Manufacturing in China vs. Vietnam
China: The Global Leader in Bearing Production
China is the world’s largest producer and exporter of bearings, with approximately 2,997 bearing manufacturers operating in 2024, showing a 1.3% increase from the previous year (IBISWorld). These manufacturers range from small-scale producers to industry giants supplying high-precision bearings for automotive, aerospace, industrial machinery, and high-tech applications.
The Chinese bearing industry generated over $45 billion in revenue in 2023, with a steady annual growth rate of 5-7% over the past decade.
Vietnam: A Developing Bearing Market
Vietnam’s bearing manufacturing industry is still in its infancy. While the country has attracted foreign investment in assembly plants, it lacks domestic high-end bearing manufacturers. In 2024, Vietnam’s total bearing market was valued at $329 million, with a 5% year-over-year increase (IndexBox). However, most of this market is reliant on imports from China, Japan, and Europe rather than domestic production.
Key takeaway: China remains the dominant force in bearing manufacturing, while Vietnam is still developing its industry, with a focus on lower-end products.
2. China’s Bearing Export Growth Over the Past Decade
Despite global trade uncertainties, China’s bearing export market has grown consistently over the past ten years. The chart below illustrates the steady rise in China’s bearing exports from 2014 to 2024.
Key insights:
In 2014, China exported 360,000 metric tons of bearings.
By 2024, this figure increased to 535,812 metric tons, demonstrating a steady upward trend.
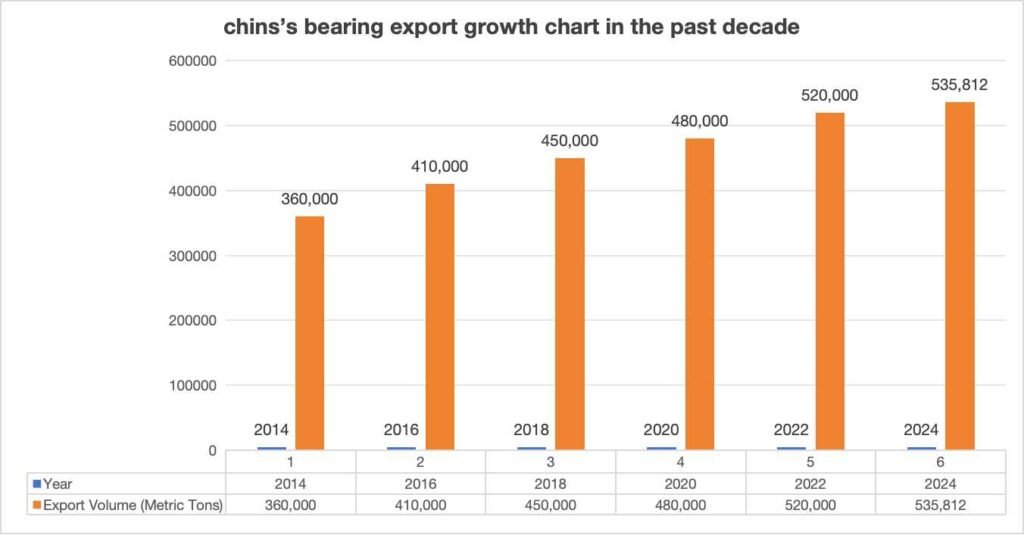
Despite geopolitical challenges, China has expanded into new international markets, reinforcing its position as a reliable supplier.
3. Advantages of China’s Perfect Supply Chain in Bearing Manufacturing
China’s fully integrated supply chain is a key advantage that Vietnam cannot match. The country has developed a highly efficient network of raw material suppliers, component manufacturers, logistics providers, and skilled labor, making it the world’s most competitive bearing production hub.
Key advantages of China’s supply chain:
✅ Abundant Raw Materials – China is one of the largest producers of high-quality bearing steel, reducing dependence on imports.
✅ Comprehensive Component Ecosystem – China has thousands of specialized factories producing rollers, cages, seals, lubricants, and housings, ensuring seamless production.
✅ Advanced Logistics Infrastructure – With world-class highways, rail networks, and ports, China ensures fast and cost-effective global shipping.
✅ Strong Supplier Collaboration – The presence of industrial clusters in cities like Wuxi, Luoyang, and Changzhou allows manufacturers to innovate and optimize costs.
In contrast, Vietnam’s supply chain is fragmented, requiring most raw materials and components to be imported, increasing costs and production times.
4. China’s Advantages in Specific Bearing Types and Industry Adoption
China’s Strength in Key Bearing Categories
Chinese bearing manufacturers have developed strong expertise in producing high-quality, cost-effective bearings across several key categories:
✅ Deep Groove Ball Bearings – Used in electric motors, home appliances, and automotive applications, Chinese manufacturers have improved precision and lifespan, making them a competitive alternative to international brands.
✅ Tapered Roller Bearings – Widely adopted in heavy machinery, trucks, and rail transport, these bearings are produced at scale in China with competitive pricing and high durability.
✅ Spherical Roller Bearings – Critical for industrial applications such as mining, steel mills, and power plants, China’s advancements in metallurgy and heat treatment have enhanced performance.
✅ Ceramic Bearings – High-performance bearings for aerospace, medical equipment, and high-speed applications, with increasing adoption of domestically produced ceramic materials.
✅ Precision Bearings – Used in robotics, CNC machines, and semiconductor manufacturing, Chinese companies have improved accuracy to compete with high-end Japanese and European brands.
Industries That Have Replaced International Brands with Chinese Bearings
Several industries have successfully shifted to Chinese-made bearings, reducing costs without compromising quality:
✅ Automotive Industry – Many domestic and international car manufacturers, including electric vehicle (EV) brands, now use Chinese bearings due to improvements in reliability and performance.
✅ Wind Energy Sector – Chinese wind turbine manufacturers, as well as global companies operating in China, have increasingly adopted locally produced bearings for cost efficiency and supply chain stability.
✅ Railway and Metro Systems – Major rail infrastructure projects in China and abroad are incorporating Chinese bearings, which meet stringent safety and durability requirements.
✅ Industrial Machinery and Automation – Manufacturers of heavy equipment, robotics, and CNC machines have adopted Chinese precision bearings to optimize costs while maintaining high performance.
✅ Construction and Mining Equipment – Due to advancements in load-bearing capacity and durability, many global companies operating in construction and mining have integrated Chinese bearings into their supply chains.
5. Workforce and Talent Advantages in China’s Bearing Industry
One of China’s greatest strengths is its highly skilled workforce. The country has over 1.2 million professionals employed in the bearing industry, including engineers, technicians, and specialized workers trained in precision manufacturing.
Key advantages of China’s bearing industry workforce:
Over 1,500 technical colleges and universities offer specialized training in mechanical engineering, industrial automation, and materials science.
Advanced training programs ensure continuous skill development, particularly in CNC machining, robotics, and AI-driven production.
A mature apprenticeship system that allows new talent to gain hands-on experience from industry veterans.
In contrast, Vietnam faces talent shortages, with most skilled engineers working in electronics and general manufacturing rather than high-precision industries like bearings.
6. China’s Manufacturing Stability and Infrastructure Advantages
China’s status as the world’s largest manufacturing powerhouse is backed by its stable political environment, reliable infrastructure, and strong government support, providing unmatched advantages for bearing manufacturers.
Key factors ensuring manufacturing stability:
Stable Political Environment – Government policies support industrial development, including tax incentives for high-tech manufacturing.
Reliable Power Supply – Unlike many emerging markets, China has a stable and extensive power grid, preventing disruptions in production.
Industry Clusters and Innovation Hubs – Cities like Changzhou and Wuxi specialize in bearing R&D, ensuring technological leadership.
Government-Backed R&D – Funding for smart manufacturing, automation, and AI-driven quality control ensures that China remains competitive.
7. Investment Trends of Global Bearing Giants in China
Despite global supply chain shifts, major international bearing brands continue to expand their investments in China. Leading companies such as SKF, NSK, FAG, NTN, TIMKEN, JTEKT, and KOYO have reaffirmed their long-term commitment to China rather than relocating to other countries.
Recent investment highlights:
SKF: Invested $120 million in expanding its Shanghai facility in 2023.
NSK: Opened a new R&D center in Suzhou to develop next-generation bearing technologies.
TIMKEN & NTN: Upgraded manufacturing automation to increase efficiency and reduce costs.
These continued investments disprove the misconception that China is losing its competitive edge in bearing manufacturing.
8. Future Outlook: Where Should You Buy Bearings?
Given the data and industry trends, China remains the top choice for bearing procurement for the next decade. Key reasons include: ✅ Unmatched manufacturing scale and expertise ✅ A well-established, efficient, and cost-effective supply chain ✅ Continued investment from global brands ✅ Advanced technological capabilities and automation ✅ Stable infrastructure and political support for manufacturing
Vietnam’s Future Potential
Vietnam may emerge as a low-end bearing supplier over the next decade, but it currently lacks the supply chain depth, skilled workforce, and high-tech manufacturing expertise needed to compete with China.
Final Recommendation
For businesses seeking high-quality, cost-effective, and technologically advanced bearings, China remains the superior choice. While Vietnam is making progress, it is still years away from being a serious competitor in high-precision bearing manufacturing.
Foreign buyers should carefully evaluate their long-term needs, quality requirements, and supply chain efficiency before shifting sourcing strategies.
Continue reading:
Top 10 Bearing Manufacturers in China.