Bearings are an important part of humanoid robot kits. There are many types of bearings involved, and their complexity is self-evident. Choosing the right bearings for a humanoid robot is essential to ensure smooth, precise, and efficient movement. The choice of bearings depends on the specific joints or parts of the robot, the loads it will bear, the required speed, the type of movement, and eSnvironmental factors. This article is a detailed explanation of how to choose bearings for each key part of a humanoid robot based on the various joints and parts of the humanoid robot.
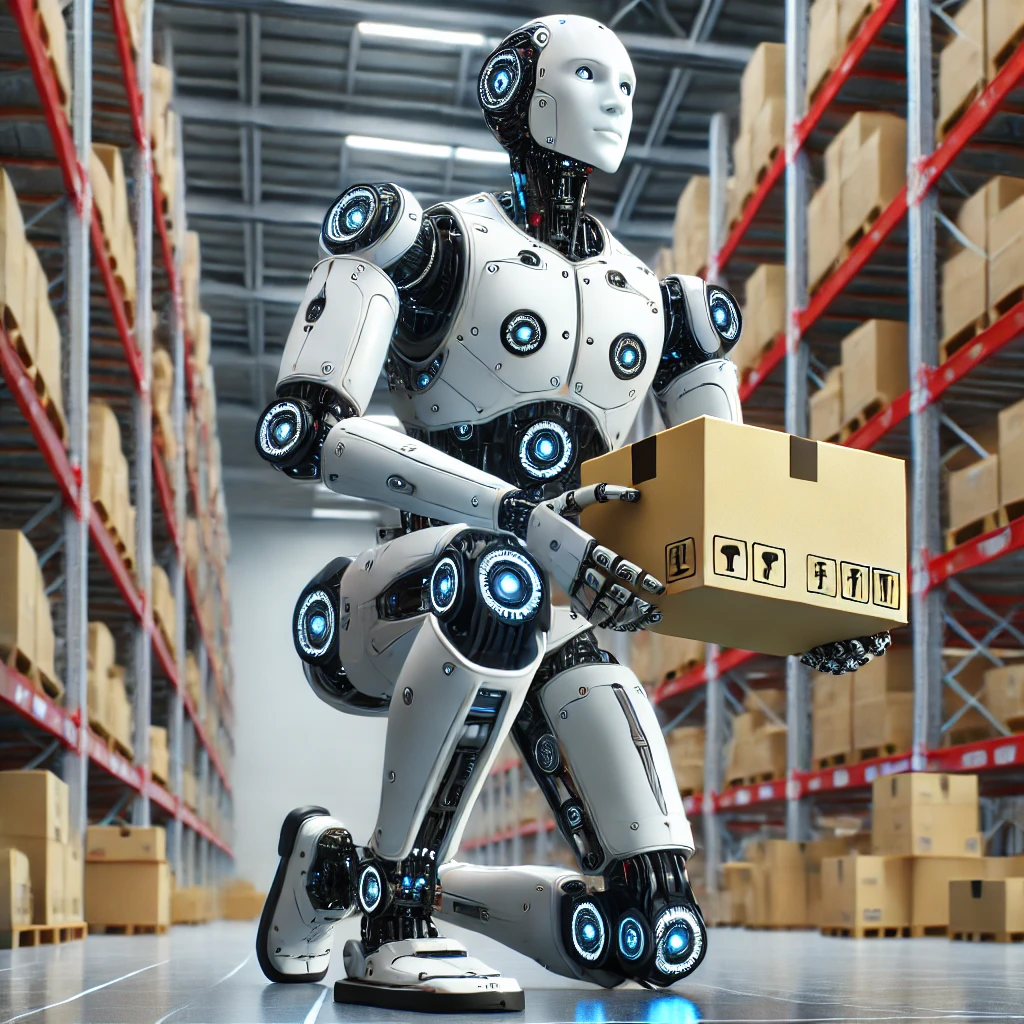
1. Head/Neck
– Key Requirements: Precision, smooth rotation, minimal friction.
– Bearing Selection:
– Ball Bearings: Small ball bearings are ideal for the head/neck joints. They provide smooth rotation and minimal friction, enabling controlled tilting and turning of the head. Since the neck moves slowly and doesn’t bear heavy loads, small and light bearings are sufficient.
– Type: Deep groove ball bearing or angular contact ball bearing.
– Why: Ball bearings offer low friction and high precision, which are crucial for the fine movements of the head and neck.
2. Shoulders
– Key Requirements: High load capacity, smooth arm rotation, and flexibility.
– Bearing Selection:
– Ball Bearings or Roller Bearings: The shoulder joint bears a significant amount of load from arm movement. Ball bearings are effective for general use, while cylindrical or tapered roller bearings might be used in higher load situations.
– Type: Angular contact ball bearings, cylindrical roller bearings.
– Why: These bearings provide smooth rotation while handling the radial and axial loads generated during arm movements.
3. Elbows
– Key Requirements: Bending and extending motion, moderate load support, precision.
– Bearing Selection:
– Angular Contact Ball Bearings or **Tapered Roller Bearings: These bearings are ideal for supporting bending motions in the elbow while maintaining smooth operation under moderate to heavy loads.
– Type: Angular contact ball bearings, tapered roller bearings.
– Why: The elbow joint must handle both radial (from arm weight) and axial (from arm extension) loads, making angular contact bearings or tapered rollers suitable for the task.
4. Wrists
– Key Requirements: Precision, small size, and low friction.
– Bearing Selection:
– Small Ball Bearings: Small ball bearings are perfect for wrist joints as they provide smooth, precise rotational movement with low friction.
– Type: Deep groove ball bearings, miniature ball bearings.
– Why: The wrist joint requires high precision but is not exposed to heavy loads, making miniature ball bearings ideal for supporting delicate, fine motor movements.
5. Hips
– Key Requirements: High load-bearing capacity, smooth rotation for walking, and balancing.
– Bearing Selection:
– Cylindrical Roller Bearings or Slewing Bearings: These bearings are suitable for large, high-load joints like the hips, where significant torque is generated during walking and balancing.
– Type: Cylindrical roller bearings, slewing ring bearings.
– Why: The hip joints bear a significant amount of the robot’s weight and support complex movement patterns. These bearings handle both axial and radial loads effectively.
6. Knees
– Key Requirements: Bending and extending motions, support for high axial loads.
– Bearing Selection:
– Angular Contact Ball Bearings or Tapered Roller Bearings: These bearings provide precise control for knee movement while handling axial loads during bending and straightening.
– Type: Angular contact ball bearings, tapered roller bearings.
– Why: The knee joints bear the weight of the body during walking and require bearings that can manage high forces and provide smooth bending motions.
7. Ankles
– Key Requirements: Fine movement for balancing and walking, low friction.
– Bearing Selection:
– Needle Bearings or Ball Bearings: Needle bearings are ideal for tight spaces and handling light to moderate loads. Ball bearings can be used where more precise motion is needed.
– Type: Needle roller bearings, deep groove ball bearings.
– Why: The ankle joints require flexibility and precision. Needle bearings allow for smooth, low-friction movement in small spaces, which is critical for stable walking and standing.
8. Fingers and Hands
– Key Requirements: High precision, low load-bearing, fine motor movement.
– Bearing Selection:
– Miniature Ball Bearings or Needle Bearings: These bearings provide smooth motion in the fingers and hands, essential for tasks like gripping and manipulating objects.
– Type: Miniature ball bearings, needle roller bearings.
– Why: The finger joints require bearings that can handle delicate, precise movements without adding much size or weight.
9. Waist (Torso)
– Key Requirements: Rotation, flexibility, and load distribution.
– Bearing Selection:
– Large Ball Bearings or Slewing Bearings: These bearings handle both radial and axial loads, facilitating smooth torso rotation and bending motions.
– Type: Slewing bearings, four-point contact ball bearings.
– Why: The waist joint needs to rotate the upper body, and the bearings must support both rotational and lateral movements while bearing the weight of the torso.
10. Actuators (Motors)
– Key Requirements: Reduced friction, increased efficiency, and durability.
– Bearing Selection:
– Ball Bearings or Roller Bearings: Bearings inside actuators and motors minimize friction and increase the lifespan of the motors that control joint movements.
– Type: Deep groove ball bearings, angular contact bearings.
– Why: Bearings in actuators help reduce mechanical losses, ensuring that the robot’s movements are energy-efficient and durable.
11. Feet (Foot Mechanism)
– Key Requirements: Flexibility, stability, and smooth transition during walking.
– Bearing Selection:
– Ball Bearings or Slewing Bearings: These bearings allow smooth foot movements, enabling the robot to adjust its stance while walking or balancing.
– Type: Ball bearings, slewing ring bearings.
– Why: The foot joint must adjust the robot’s posture, making bearings essential for fluid and precise movements when the robot is walking or standing.
12. Internal Rotating Components
– Key Requirements: High precision, minimal friction, and continuous operation.
– Bearing Selection:
– Ball Bearings or Magnetic Bearings: Bearings are used in internal rotating components such as sensors or encoders. Magnetic bearings may be used in high-precision areas to avoid friction altogether.
– Type: Ball bearings, magnetic bearings.
– Why: These bearings support precise, high-speed motion without causing friction, ensuring optimal sensor performance or internal rotational mechanisms.
Conclusion
When choosing bearings for a humanoid robot, it’s crucial to match the bearing type with the specific joint’s function, load, speed, and precision requirements. Ball bearings and roller bearings are commonly used for general rotation and high-load joints like the shoulders and hips, while needle bearings and miniature ball bearings are ideal for small, precise movements in areas like the fingers and wrists. Slewing bearings are suitable for large, high-load joints such as the waist and hips. By selecting the right bearing for each part, the robot can achieve smooth, efficient, and durable movement. If you have any questions about the selection of robot bearings, please send us an email and the professional engineers of the bearing manufacturer VKUKEN will provide you with any help.