According to the production needs, some machine tools need to continue to work at high speed, but sometimes because of the failure of the high speed spindle bearing, the equipment can not operate normally. There are many reasons for the failure of high-speed spindle bearings, which must be targeted to solve the problem, then what are the general reasons?
Maxwell, a brand bearing technical engineer with 15 years of experience, wrote this article specifically to help machine tool operators.
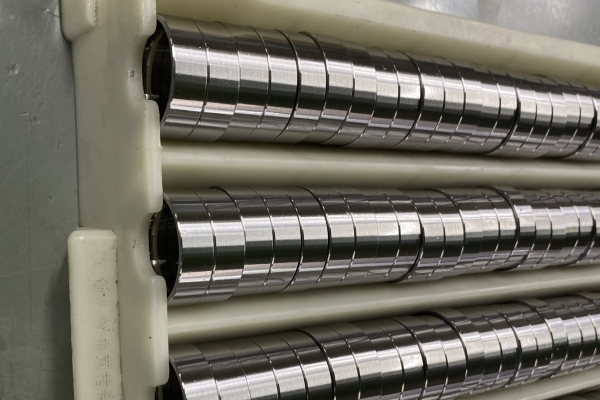
Analysis of failure causes of high speed spindle bearings
1. Lubrication problem
When the spindle of the machine tool is running at high speed, the bearing has relatively high requirements for lubrication, which can effectively reduce friction and wear. If there are problems such as insufficient lubricating oil, pollution or improper selection, the bearing surface is easy to break the lubrication film, aggravate the bearing wear, and eventually lead to failure.
2. Fatigue pitting
When angular contact ball bearings are running at high speed, the rolling body and raceway will bear very large alternating stress, and it is easy to produce fatigue pitting during long-term operation, which is one of the most common failure forms of rolling bearings. Small pits can be seen on the bearing surface, affecting the bearing performance and service life.
3. High temperature
At high speed, a lot of friction heat is generated inside the bearing. If the heat cannot be dispersed in time, the bearing exceeds the withstand temperature range, further accelerates the oxidation and deterioration of the lubricating oil, reduces the lubrication effect, and the bearing will be seriously worn and eventually fail.
4. Assembly problems
There are several assembly forms of spindle bearings of high-speed machine tools, and different combination and pairing methods will affect the service life of bearings. If the assembly has too much clearance, insufficient interference, and the mating surface is not clean, it will cause abnormal vibration and wear of bearings during operation, and the bearings will naturally fail after a long time.
In another of my articles, I detail the pairing and installation guidelines for angular contact ball bearings, which can be read by clicking on the safety link below.
5. Material fatigue
High speed spindle bearing material is prone to fatigue damage due to alternating stress for a long time, especially under high speed operation. If the quality of the material used by the machine tool spindle bearing manufacturer is not good, fatigue appears earlier, so that the bearing bearing capacity is reduced, causing bearing failure.
6. Environmental issues
High-speed spindle bearing operating environment will also cause failure, such as high temperature, high humidity, corrosive gas and so on. These harsh environmental conditions accelerate the wear and corrosion of bearings and shorten the service life of bearings.
Main shaft bearing failure avoidance measures
1, machine tool spindle bearing production bearing must choose wear-resistant, high-strength, anti-oxidation materials, from the root to improve the service life of the bearing.
2, according to the working requirements of the equipment, choose the appropriate bearing type and cage material, so that the bearing can meet the actual work needs.
3, high-speed machine spindle bearing installation method to be correct, to avoid improper installation of bearing damage, must pay attention to bearing position, shoulder processing accuracy, axis concentricity, so that the bearing position symmetry, to avoid stress concentration.
4, high-speed spindle bearing lubrication strictly implement the “five fixed” (fixed point, fixed quality, quantitative, regular, fixed person), select the appropriate lubricant, regular replacement, so that the bearing is well lubricated. In addition, regular testing of lubricating oil quality, timely replacement of unqualified lubricating oil.
Conclusion
There are many reasons for the failure of high-speed spindle bearings. If the bearing failure is found, the equipment should be stopped immediately, and the causes of failure should be gradually investigated, and then the problem should be solved. The key method to prevent bearing failure is also the maintenance frequency of equipment and bearings, and prevention can prevent problems before they happen.